The Ultimate Guide to Packaging Maker Fixing: Keep Your Workflow Running Efficiently
Understanding the intricacies of product packaging equipment repair work is vital for preserving optimal efficiency and lessening disruptions. Normal maintenance not just extends the life of these makers but also addresses typical issues that can restrain efficiency.
Importance of Normal Maintenance
Routine maintenance of product packaging machines is critical for making sure optimal efficiency and longevity. By applying a structured maintenance schedule, operators can identify possible issues prior to they intensify into considerable problems. This positive approach not just decreases downtime however additionally extends the life expectancy of the equipment, eventually leading to minimized operational expenses.
Normal inspections enable the analysis of vital parts such as seals, sensors, and belts. Resolving wear and tear quickly protects against unexpected failures that might interfere with manufacturing and lead to expensive repair work. Additionally, routine maintenance assists make certain conformity with industry criteria and policies, promoting a risk-free workplace.
Moreover, maintenance activities such as cleaning, calibration, and lubrication considerably improve maker performance. Boosted efficiency converts to regular item quality, which is important for preserving client fulfillment and brand name track record. A properly maintained product packaging maker runs at ideal rates and lowers product waste, adding to general efficiency.
Common Packaging Machine Concerns
Product packaging machines, like any type of intricate equipment, can run into a range of typical problems that might prevent their performance and effectiveness - packaging machine repair. One widespread issue is inconsistent securing, which can result in item spoilage and wastefulness if plans are not correctly sealed. This often arises from misaligned elements or worn securing aspects
One more frequent concern is mechanical jams, which can happen due to international items, used components, or inappropriate positioning. Jams can cause hold-ups in production and rise downtime, eventually affecting total performance. Furthermore, electronic breakdowns, such as failure in sensing units or control systems, can disrupt procedures and lead to incorrect dimensions or irregular device actions.
Moreover, issues with product feed can also develop, where things may not be supplied to the packaging location regularly, creating interruptions. Last but not least, wear and tear on rollers and belts can lead to suboptimal efficiency, requiring instant focus to avoid additional damages.
Recognizing these common problems is essential for maintaining the stability of product packaging procedures, guaranteeing that equipment runs efficiently and successfully, which subsequently aids in meeting production targets and preserving item top quality.
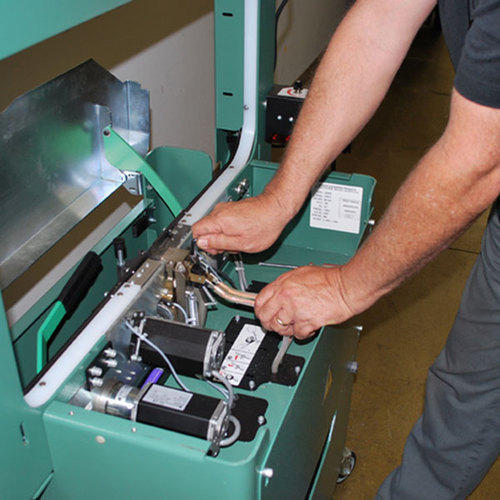
Troubleshooting Strategies
Reliable fixing techniques are crucial for immediately dealing with issues that emerge with packaging machines. A methodical method is essential for identifying the origin of malfunctions and lessening downtime. Begin by gathering details about the signs and symptoms observed; this may consist of unusual sounds, operational hold-ups, or error codes presented on the device's user interface.
Next, describe the device's guidebook for troubleshooting guidelines particular to the version in concern. This source can offer beneficial insights right into usual issues and advised diagnostic steps. Utilize aesthetic inspections to look for loosened connections, worn belts, or misaligned parts, as these physical factors commonly add to operational failings.
Apply a procedure of removal by testing individual maker features. For circumstances, if a seal is not forming correctly, assess the securing device and temperature setups to figure out if they satisfy functional specifications. Document each action taken and the outcomes observed, as this can aid in future troubleshooting efforts.
Repair work vs. Substitute Choices
When faced with devices breakdowns, deciding whether to replace a packaging or repair equipment can be a complex and vital selection. This choice rests on several essential aspects, including the age of the device, the degree of the damages, and the forecasted effect on functional performance.
First of all, take into consideration the machine's age. Older devices may need more constant repairs, bring about higher advancing expenses that can exceed the investment in a new unit. Furthermore, examine the severity of the breakdown. Small problems can commonly be dealt with promptly and cost effectively, whereas considerable damages could necessitate a substantial monetary commitment for repairs.
Operational downtime is one more vital consideration. If fixing the device will trigger extended delays, purchasing a brand-new equipment that provides enhanced performance and reliability could be much more prudent. Take into consideration the accessibility of components; if substitute parts are difficult to come by, it might be a lot more tactical to change the machine entirely.
Inevitably, executing a cost-benefit evaluation that consists of both instant and long-lasting ramifications will certainly assist in making a notified decision that straightens with your operational objectives and financial constraints. (packaging machine repair)
Preventative Actions for Durability

Trick precautionary steps consist of routine lubrication of moving parts, placement checks, and calibration of controls and sensing units. Establishing a cleaning timetable to remove debris and impurities from machinery can considerably reduce wear and tear (packaging machine repair). In addition, keeping track of operational criteria such as temperature level and resonance can help discover abnormalities beforehand
Educating staff to identify signs of wear or malfunction is one more important element of precautionary upkeep. Encouraging operators with the understanding to execute visit our website basic troubleshooting can result in quicker resolutions and reduce operational disturbances.
Paperwork of upkeep tasks, consisting of service documents and assessment findings, promotes responsibility and promotes notified decision-making relating to repair services and replacements. By focusing on safety nets, organizations can guarantee their packaging makers run at peak performance, inevitably bring about raised efficiency and lowered functional costs.
Verdict
Finally, the effective repair and maintenance of packaging makers are vital for maintaining functional performance. Normal maintenance mitigates the threat of common concerns, such as inconsistent securing and mechanical jams, while organized troubleshooting methods help with timely resolution of breakdowns. Furthermore, cautious factor to consider of repair work versus replacement decisions adds to affordable monitoring of resources. By applying precautionary procedures, services can boost device durability and guarantee click to find out more uninterrupted performance in product packaging operations.
Understanding the complexities of product packaging machine fixing is critical for maintaining ideal efficiency and lessening disturbances.Routine maintenance of product packaging makers is crucial for guaranteeing optimal performance and longevity.Packaging machines, like any kind of complicated equipment, can encounter a selection of common issues that may hinder their performance and efficiency. If repairing the device will trigger extended delays, spending in a new maker that supplies boosted performance and integrity could be a lot more prudent.In verdict, the efficient upkeep and repair service of product packaging devices are critical for sustaining functional effectiveness.